PPM (Planned and Preventative Maintenance)
Planned and Preventative Maintenance (PPM) is maintenance carried out on machinery, equipment, plants, buildings, or grounds per predefined schedules, based on either fixed time periods or the actual usage of the equipment.
The most effective way of preventing unexpected failures is to implement an ongoing programme of planned maintenance. Regular care and condition monitoring not only keeps equipment operational through the scheduling of vital cleaning, lubrication, and calibration tasks but also ensures incipient faults are picked up during visual inspections.
The PPM Planner and PPM Active Tasks List allow you to assign resources, generate orders where required, record time, manage related issues, and eventually complete tasks.
K2 can assist in monitoring PPM Tasks by indicating and reporting on ones that are due, in progress or overdue.
There are three methodologies for undertaking PPM Tasks:
Direct Labour – the organisation manages PPM Tasks and undertakes the work using internal operatives
Outsourced Tasks – the organisation manages PPM Tasks and instructs contractors to undertake the work when it is due
Outsourced PPM – the organisation outsources PPM, including management, inspections, remedial work, and audit
The PPM data structure is configured in multiple ways to support the organisations objectives. The diagram below details different configurations for PPM entities, but any combination can be used depending on the PPM methodology and data structure.
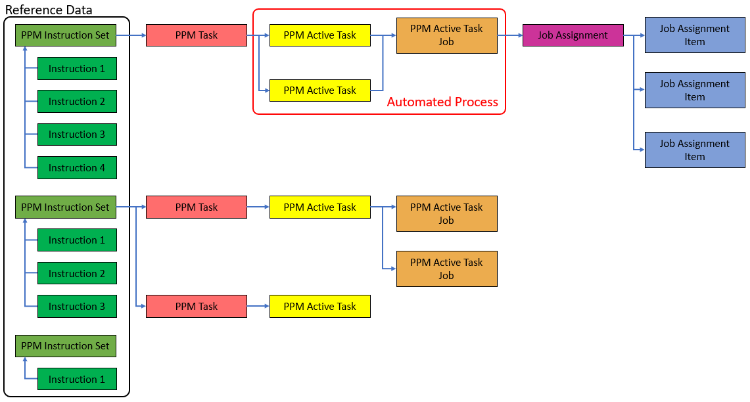
The blocks in the diagram above are described in the following table:
Block | Description |
---|---|
PPM Instruction Set | A record that groups together all of the individual PPM Instructions. It also includes default information such as the PPM family, required stock items, schedule and a summary of time and cost to complete the instructions. They are assigned to one or more PPM Tasks. |
PPM Instructions | These are defined in Instruction Set reference data and detail the specific checks, inspections, tasks and services that need to be carried out. A resource count, time and cost are assigned to each instruction. |
PPM Task | A record that groups the PPM Instruction Set, schedule, location and or asset or component and the cost code. Related Restrictions and Warnings (R&W) and asbestos in the PPM location are also displayed. |
PPM Active Task | A record of the task for the specific location, asset or component. When there are multiple locations, assets or components linked to a PPM Task, one PPM Active Task is created for each. PPM Active Tasks are created by an automated process as and when they are due. |
PPM Active Tasks Job | The record for the work that needs to be carried out. If there are multiple PPM Active Tasks created from the PPM Task only one PPM Active Task Job is created, each instruction, in each location is itemised on the job record. Multiple jobs can be created for the same PPM Active Task if more than one person is going to undertake the work. However, the individual instructions are split across the jobs so they are not duplicated. |
Job Assignment | Created when the job is assigned to an operative. The job assignment tracks the status of the job which the operative is undertaking. |
Job Assignment Item | The individual instruction on K2 Mobile that needs to be carried out, each has a status of whether it has been completed. |
Related Topics
Click the links below to navigate to the following related topics: